智能制造新篇章:机器人上下料系统扮演关键角色
Jun 23,2025
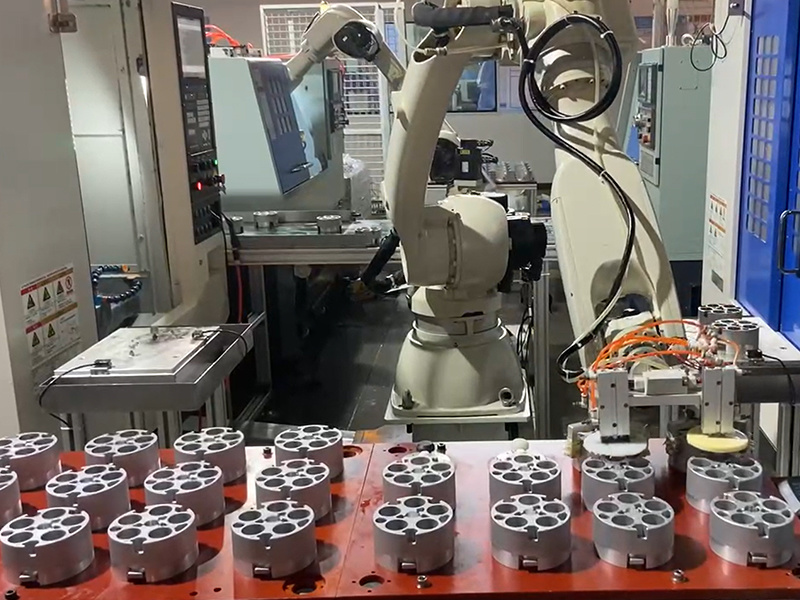
制造业的生产流程中,上下料环节作为生产准备的关键步骤,其效率与准确性直接影响到整体生产进度。传统的人工上下料方式,不仅受限于工人的体力与工作时长,难以满足长时间、高强度的生产需求,而且在操作精度上存在较大波动,容易因人为失误导致产品质量问题。随着工业自动化的发展,机器人上下料系统应运而生,逐步成为制造业生产线上的 “标配”。
机器人上下料系统由机器人本体、控制系统、视觉识别系统和物料输送装置等核心部分组成。机器人本体通常采用多关节机械臂,具备灵活的运动能力和强大的负载能力,能够在复杂的生产环境中快速、准确地抓取和放置物料。例如,在汽车零部件加工车间,大型的六轴机器人可以轻松抓起重达数十公斤的发动机缸体,精确地放置到加工设备的工作台上,其重复定位精度可达 ±0.05 毫米,确保了加工位置的准确性。
控制系统作为机器人上下料系统的 “神经中枢”,通过预设的程序和算法,精确控制机器人的运动轨迹和动作顺序。同时,它还能与生产设备的控制系统进行实时通信,根据设备的加工进度和物料需求,协调机器人的上下料节奏。当加工设备完成一个工件的加工后,控制系统会立即指令机器人进行下料操作,并将新的物料送上加工台,实现生产过程的无缝衔接,大大缩短了设备的待机时间,提高了生产效率。
视觉识别系统赋予了机器人 “眼睛”,使其能够准确识别物料的位置、姿态和形状。通过安装在生产线关键位置的高清摄像头和先进的图像识别算法,机器人可以在物料输送过程中,快速定位目标物料,并计算出最佳的抓取路径。在电子元器件生产中,由于元器件尺寸微小、形状各异,对抓取精度要求极高,视觉识别系统能够识别到微米级的尺寸差异,引导机器人精准抓取,避免因抓取偏差导致元器件损坏。
物料输送装置则负责将物料有序地输送到机器人的工作范围内,常见的有皮带输送机、链式输送机和 AGV(自动导引车)等。这些输送装置与机器人紧密配合,根据生产节奏和物料需求,实现物料的连续、稳定供应。在一些大型机械制造企业的生产车间,AGV 小车会按照预设路线,将原材料自动运输到机器人上下料工作站,机器人完成上下料操作后,AGV 再将加工好的工件运送至下一道工序,整个过程无需人工干预,实现了物料运输与上下料的全自动化。
在实际应用中,机器人上下料系统带来的效益十分显著。在五金加工行业,引入机器人上下料系统后,单台设备的日产量提升了 50% 以上,产品合格率从原来的 85% 提高到 98%。同时,由于机器人可以 24 小时不间断工作,企业能够充分利用设备的生产能力,有效降低了单位产品的生产成本。在高危作业环境,如高温铸造车间、有毒化工生产车间,机器人上下料系统更是发挥了不可替代的作用,它避免了工人直接接触危险环境,极大地保障了员工的生命安全,减少了企业的安全风险。
随着人工智能、5G 等新技术的不断融合,机器人上下料系统未来将朝着更加智能化、柔性化的方向发展。例如,借助人工智能技术,机器人可以实现自主学习和决策,根据不同的物料和加工工艺,自动优化上下料策略;5G 技术的应用则能够实现机器人与生产系统的实时、高速通信,进一步提升系统的响应速度和协同能力。机器人上下料系统将在制造业智能化升级的道路上发挥更加重要的作用,推动行业向更高质量、更高效益的方向迈进。
上一个:
下一个:
最新新闻